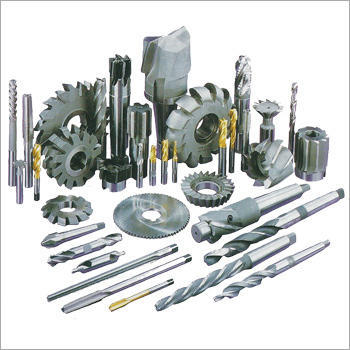
عدد القطع
أدوات القطع
يتم تصنيف أدوات القطع المعدنية كنقطة مفردة أو متعددة النقاط. يمكن استخدام أداة القطع أحادية النقطة لزيادة حجم الثقوب أو الثقب. يتم تنفيذ الخراطة والمملة في المخارط والمصانع المملة. أدوات القطع متعددة النقاط لها حافتان أو أكثر للقطع وتشمل قواطع الطحن والمثاقب والدبابيس.
هناك نوعان من العمليات. إما أن الأداة تتحرك في مسار مستقيم مقابل قطعة العمل الثابتة ، كما هو الحال في المشكل ، أو أن قطعة العمل تتحرك عكس الأداة الثابتة ، كما هو الحال في المسوي. يجب توفير زوايا ارتياح أو خلوص لمنع سطح الأداة الموجود أسفل حافة القطع من الاحتكاك بقطعة العمل. غالبًا ما يتم توفير زوايا أشعل النار على أدوات القطع لإحداث حركة إسفينية في تكوين الرقائق وتقليل الاحتكاك والحرارة.
مواد الأدوات
لإزالة الرقائق من قطعة العمل ، يجب أن تكون أداة القطع أصعب من قطعة العمل ويجب أن تحافظ على حافة القطع عند درجة الحرارة الناتجة عن احتكاك عملية القطع.
الكربون الصلب
كان الصلب الذي يحتوي على نسبة كربون تتراوح من 1 إلى 1.2 في المائة من أقدم المواد المستخدمة في أدوات الآلات. تعتبر الأدوات المصنوعة من الفولاذ الكربوني غير مكلفة نسبيًا ولكنها تميل إلى فقدان القدرة على القطع عند درجات حرارة تبلغ حوالي 400 درجة فهرنهايت (205 درجة مئوية).
حديدعالى السرعه
في عام 1900 ، سمح إدخال الفولاذ عالي السرعة بتشغيل الأدوات بضعف أو ثلاثة أضعاف السرعة المسموح بها مع الفولاذ الكربوني ، وبالتالي مضاعفة أو مضاعفة سعة ورش الآلات في العالم. أحد أكثر أنواع الفولاذ عالي السرعة شيوعًا يحتوي على 18 في المائة من التنجستن ، و 4 في المائة من الكروم ، و 1 في المائة من الفاناديوم ، و 0.5 إلى 0.8 في المائة فقط من الكربون.
سبائك الصب
تم تطوير عدد من مواد أدوات القطع المصنوعة من السبائك المصبوب ؛ تحتوي هذه السبائك اللاحديدية على الكوبالت والكروم والتنغستن وهي فعالة بشكل خاص في اختراق الجلد الصلب على الحديد الزهر والاحتفاظ بقدرتها على القطع حتى عندما يكون أحمر حارًا.
كربيد التنجستن الأسمنتي
تم استخدام هذه المادة لأول مرة لقطع المعادن في ألمانيا في عام 1926. المكون الرئيسي لها هو كربيد التنجستن المقسم بدقة في مادة رابطة من الكوبالت ؛ صلابته تقترب من صلابة الماس. يمكن تشغيل أدوات كربيد التنجستن بسرعات قطع أعلى بعدة مرات من تلك المستخدمة مع الفولاذ عالي السرعة.
أكاسيد
تعتبر أطراف الأدوات الخزفية أو الأكسيد واحدة من أحدث التطورات في مواد أدوات القطع. تتكون بشكل أساسي من حبيبات أكسيد الألومنيوم الدقيقة ، والتي ترتبط ببعضها البعض.
الماس
تم استخدام الماس لسنوات عديدة لتصحيح عجلات الطحن ، وفي قوالب سحب الأسلاك ، وكأدوات القطع. بالنسبة لتطبيقات القطع ، يتم استخدامها إلى حد كبير لأخذ قطع التشطيب الخفيفة بسرعة عالية على المواد الصلبة أو الكاشطة وللمحامل البرونزية والمعدنية المملة للإنهاء.