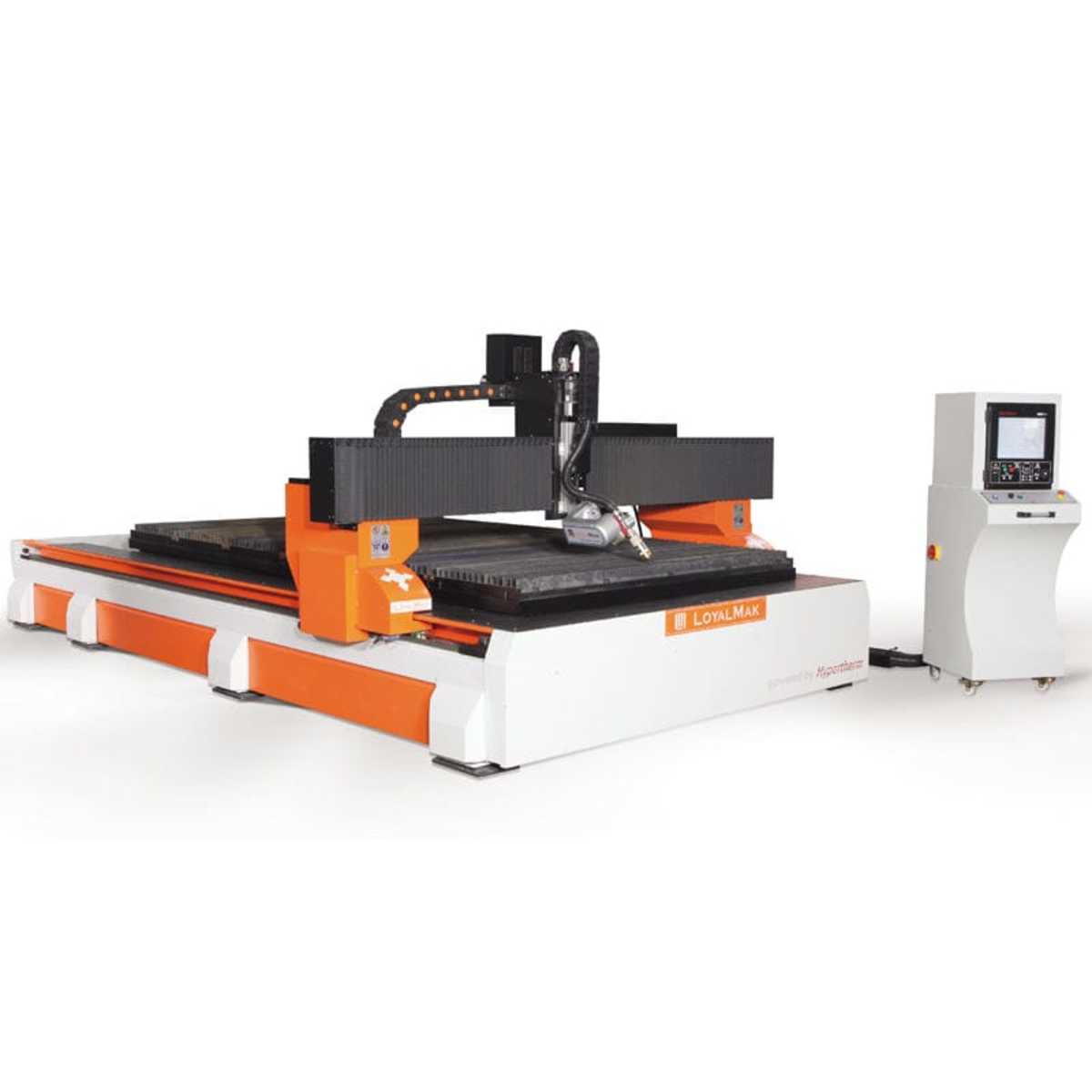
ماهي ماكينة القطع بالبلازما؟
يتم استخدام قطع البلازما باستخدام الحاسب الآلي لقطع الأشكال والخطوط من خلال السماكة الكاملة للصفائح المسطحة أو الصفائح المعدنية ومن خلال سماكة الجدار للأقسام مثل الأنابيب والعوارض الهيكلية. هذا هو ناتج ملف تعريف ثنائي الأبعاد أو قسم ملف شخصي حصل على قطع البلازما ، وهو التصنيف العام كعملية "تحديد".
أطلق العنان لـ CNC Plasma مع شبكة التصنيع
يتم تسخين البلازما بالغاز بشكل أساسي بواسطة قوس كهربائي لتكوين حزمة بلازما قادرة على إذابة المعدن على الفور تقريبًا. يشكل مزيج حرارة البلازما ، وضغط التيار المركز للغاز آلية القطع - تذوب البلازما من خلال سمك المادة ، بينما يزيل ضغط الغاز المادة المنصهرة.
تكوينات قطع البلازما باستخدام الحاسب الآلي
يمكن تقسيم قدرة القطع بالبلازما CNC إلى 3 مجموعات رئيسية يمكن العثور عليها في جميع أنحاء المملكة المتحدة ، متفاوتة في أشكال المخزون وعدد محاور التحكم المتاحة. لذلك دعونا ندخله ...
2D قطع البلازما
وتسمى أيضًا قطع البلازما المسطح ، وتنتج ملفات تعريف مسطحة من اللوح أو الصفائح ، مع حواف مستقيمة عند 90 درجة إلى سطح المظهر الجانبي. عادة ، يتم تكوين أسرة قطع البلازما عالية الطاقة بهذه الطريقة ، مما يمنح أكبر عمق قطع يتراوح بين 100-150 مم.
التنميط 2D البلازما
قطع بلازما ثلاثي الأبعاد
على غرار قطع البلازما ثنائي الأبعاد ، ويشار إليه أيضًا باسم قطع البلازما المسطح ، يضيف هذا الاختلاف بعدًا ثالثًا من خلال إدخال قطع زاوي أو حافة مشطوفة من خلال الورقة أو مادة اللوحة. عادة ، يتم تكوين أسرة قطع البلازما عالية الوضوح بهذه الطريقة ، مما يمنح أكبر قدر من المرونة والدقة و / أو السرعة.
3 قطع بلازما الأبعاد
قطع الأنبوب والقسم بالبلازما
إن مادة المخزون ومحاور القطع هي التغييرات والتحسينات الرئيسية بالمقارنة مع قطع البلازما ذي القاعدة المسطحة. عادة ما يكون رأس قطع البلازما ثابتًا بينما يتم مناورة القسم أو الأنبوب تحت الشعاع مما يؤدي ليس فقط إلى إنشاء ملفات تعريف نهاية ، ولكن فتحات وعلامات وثقوب داخل القسم أو الأنبوب.
قد تكون هذه الآلات أو لا تكون مزودة برأس مائل أو المحور الثالث ، مما لا يسمح فقط بقطع القسم ، ولكن أيضًا شطب حوافه أو ثقب الثقوب - كما هو موضح أعلاه "قطع البلازما ثلاثية الأبعاد" الموصوفة أعلاه
قطع الأنبوب والمقطع بالبلازما
ما هي عمليات قطع البلازما المرافقة نوعياً؟
التصنيع ، الانحناء ، الدرفلة ، اللحام ...
يستخدم قطع البلازما عادة لقطع التشكيلات المستخدمة في التصنيع ، بما في ذلك الانحناء والدرفلة واللحام. في تصنيع الأنابيب والمقاطع ذات القطر الكبير ، من الممكن قطع مقاطع نهاية الأنبوب البلازمي ، وقطع الثقوب والتقاطعات من مادة اللوحة المسطحة جزئيًا. في وقت لاحق ، عندما يتم لف الملف الشخصي المسطح ثم يلحم اللحام ، لا يتطلب الأنبوب المتشكل أي شكل آخر ، بخلاف قطع الثقوب والوصلات المقطوعة جزئيًا.
بالقطع ...
ملفات تعريف قطع البلازما هي أيضًا مادة مخزون شائعة لمزيد من المعالجة عن طريق العديد من عمليات التشغيل. في هذه الحالة ، يعمل قطع البلازما كعملية إزالة المواد السائبة ، مما يمنح الماكينة مادة مخزون تتضمن بعض بدل المعالجة. من الممكن في كثير من الحالات أن التشكيلات تتطلب الحد الأدنى من القطع مثل الحفر والتنصت بعد قطع البلازما ، ويرجع ذلك إلى المستوى العالي من الدقة وجودة حافة القطع التي يمكن تحقيقها بقطع البلازما.
طحن المحراث ...
في الحالات التي تحتاج فيها المادة التي يتم قطعها من البلازما إلى زيادة التسطيح ، يمكن إجراء عملية الحراثة أو الطحن "Lumsden". هذا يزيد من تسطيح الملف الشخصي ، مع توفير فائدة إضافية لإزالة الجلد المادي وتنظيف مظهره. تتم معالجة الأسطح المستوية للملف الشخصي المقطوع أثناء طحن المحراث ، وتترك الحواف المقطوعة دون أن تتأثر.
تحضير الحواف ...
يسمح الرأس المائل أو المحور الثالث على آلة قطع البلازما باستخدام الحاسب الآلي بإنشاء حواف مشطوفة أو خطوط أو حواف مائلة في مادة المخزون ، سواء كانت مسطحة أو ذات مقطع ثلاثي الأبعاد. يمكن أن يكون هذا مفيدًا للغاية في الحالات التي يتم فيها تصميم أنابيب وملامح قطع البلازما لتشكيل تقاطعات زوايا ، أو مطلوب تحضيرات اللحام. ومع ذلك ، لا تقدم جميع أنظمة القطع بالبلازما CNC هذا المحور الثالث ، أو رأس مائل ، لذلك من الشائع أن تمر الملفات الشخصية بعملية تحضير الحواف بعد قطع البلازما. يمكن تطبيق هذا على طول الحافة المسطحة الطويلة للملف الشخصي ، أو الحافة المحددة لثقب أو فتحة مشكلة في أنبوب أو مقطع. باستخدام CNC Edge Preparation ، يمكن تحقيق تنوع كبير في أشكال التحضير ، على عكس القطع البسيط بزاوية ممكنة مع قطع البلازما.
تنظيف وحفظ ...
في بعض الأحيان يكون للمادة التي تتم معالجتها قشرة أو جلد يحتاج إلى إزالة ، في هذه الحالات يمكن تنظيف أو معالجة ملفات قطع البلازما بعدة طرق لتناسب احتياجاتك. يمكن استخدام عمليات التنظيف مثل التخليل أو التفجير الكاشطة ، في حين أنه من الممكن أيضًا طلاء ملفات التعريف إلى العلاقات العامة